Boxley Materials Company Breaks It, Makes It Black
BY AsphaltPro Staff
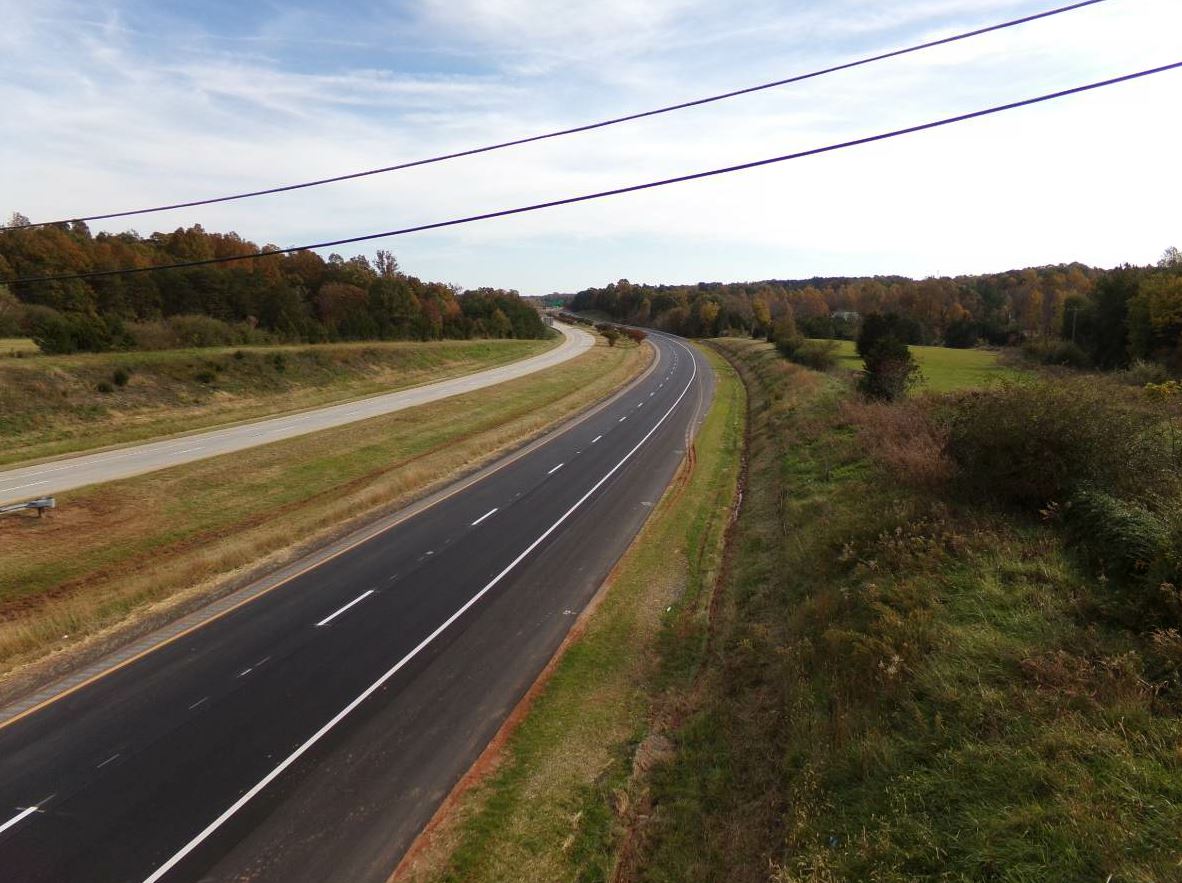
Every once in a while, there comes a job that stands out, not only to your crew, but also to the community and the asphalt industry in general.
The rubblization and rehabilitation of the 2.6 miles of two eastbound lanes on the Route 460 bypass around the historic community of Appomattox, Virginia, was that kind of job.
“This was a plain jointed concrete section of pavement built in the early ‘90s,” said Eddie Blount, chief estimator at Boxley Materials Company, Blue Ridge, Virginia.
The plain jointed concrete was meant to last 40 years, but local engineers noticed the slabs began rocking about 10 years ago. Dowells connecting the slabs didn’t transfer the load as expected, joints opened and water invaded the 9 inches of concrete and 57-inch drainage layer atop cement stabilized soil.
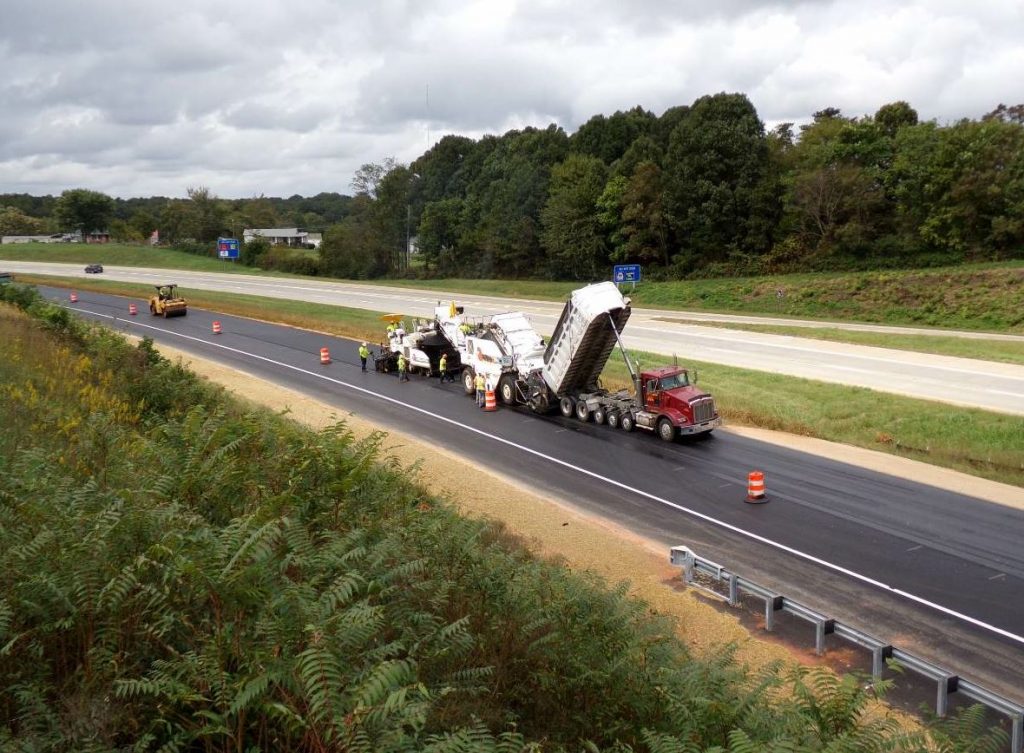
Boxley paved the final lift of 2 inches of SM-12.5D.
“Water eroded away at the cement treated soil and with that space under the slabs, it starting rocking,” said Ken Arthur, Boxley’s asphalt plant operations manager. “VDOT performed substantial repair over the last decade and the ride had degraded significantly .”
“This is a project I have been tracking since 2000,” said Virginia Asphalt Association Executive Vice President Trenton Clark. “I noticed the first failures and began investigating the potential causes. In time, I recommended rubblization to the district as a way to fix a long time maintenance issue.”
Then in March of 2017, the Virginia Department of Transportation put a more permanent solution to bid: rubblize the eastbound 25-year-old concrete pavement and pave with an asphalt overlay.
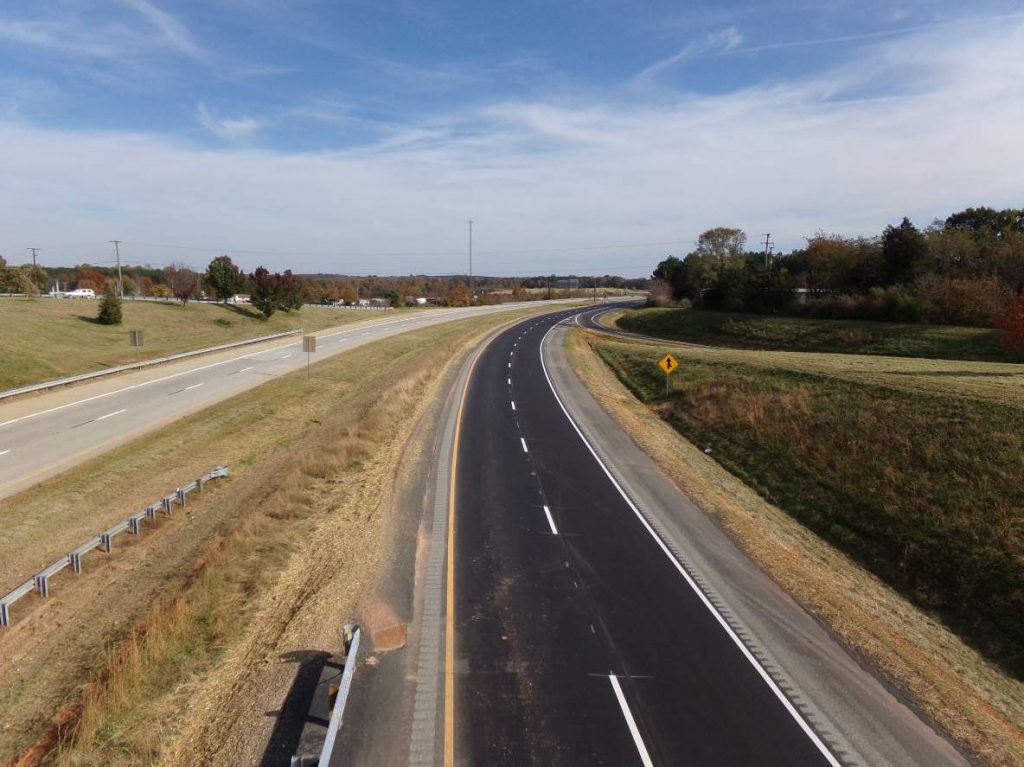
The 2.6-mile project on Route 460 included the rubblization of the existing concrete roadway and the placement of a new asphalt overlay.
Boxley, a Summit Company, was the low bidder on the $5.3 million job. They began work June 2018 and anticipate full completion by mid-October.
“By rubblizing the job, the department was able to utilize the crushed concrete as both a structural base and a drainage layer,” Arthur said. The 5.2-lane-mile job also includes ramps and turn lanes, as well as a 3-foot inside shoulder and a 10-foot outside shoulder.
“This was a VDOT-designed project, so the department had a clear understanding of what they wanted as a finished product. However, because the process was so unique to our area there were ample opportunities to partner through the learning-curve”, Blount said. “VDOT afforded us flexibility on how to execute the work and were a great partner on the project.”
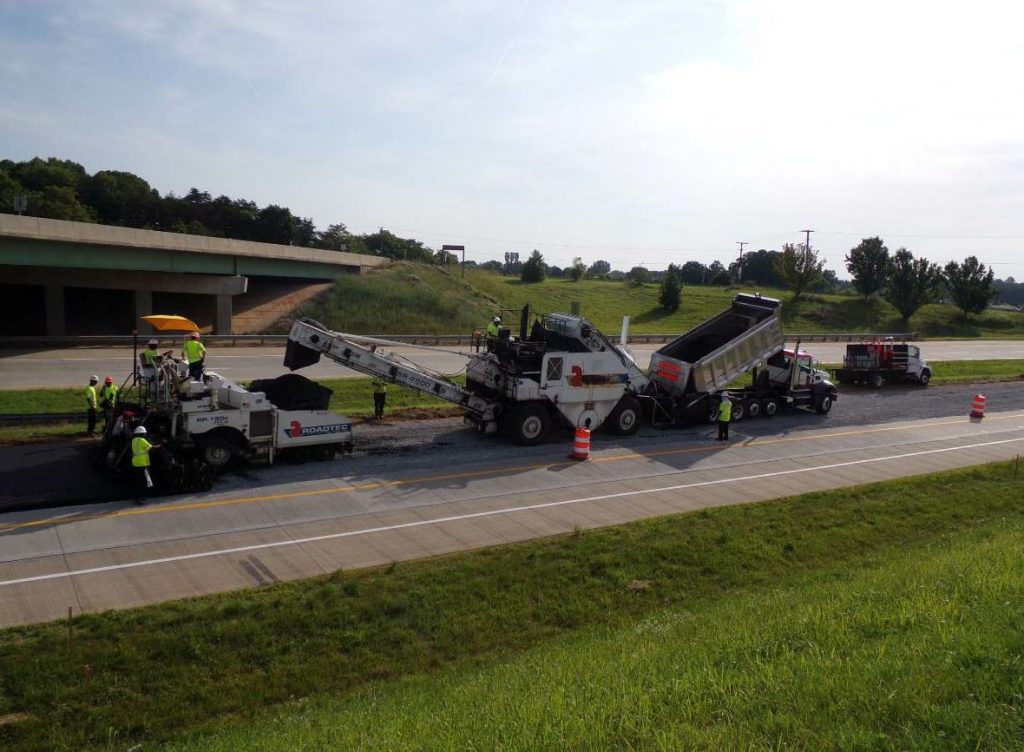
Boxley laid a total of nearly 33,000 tons of asphalt: 17,000 tons of base mix, 8,000 tons of intermediate mix, and 7,900 of surface mix.
Route 460 is an east-west high-volume primary road running from [North Hook Bend in Tidewater] to the state line with West Virginia. This section rehabilitated by Boxley is a bypass around a small town and sees around 3,500 vehicles per day.
As with most jobs, figuring out how to minimize traffic was a challenge. Boxley tackled this by shifting traffic to one lane occupying the roadway’s former right lane and outside shoulder. Then, they rubblized and paved the inside shoulder and left lane before repeating the process on the right lane and shoulder.
“The biggest benefit of doing it that way was that it gave us more room to work and made things safer for the traveling public,” said Project Manager Brian Pieklik.
When they made it to the outside lane, Boxley also had to work around four on and off ramps. They closed two, rubblized, paved and got the ramps back in use within a week, and then repeated the process with the other two.

The Boxley crew utilized a Roadtec 2500A shuttle buggy to load the paver in an effort to put less weight on the paver without shifting the rubblized surface.
Before Boxley could make the concrete pavement black, they first needed to rubblize the concrete to a depth of 12 inches in the main travel lanes and 9 inches on the shoulders.
Boxley sub-contracted the rubblization to Antigo Construction of Antigo, Wisconsin. Antigo used its MHB Badger Breaker tractor-mounted rubblizing machine, followed by a Bomag 213D Z grid steel roller.
Antigo performed breaking and initial seating of the rubblized concrete with their Z grid-patterned steel wheel roller.
“When their hammers hit the concrete, it was breaking into a lot of hand-sized pieces,” Pieklik said. “But, when their Z grid hit it, it was more like the size of a #57.” After one pass with the Z grid steel roller came a Bomag BW211D steel wheel roller for two passes and a Cat PS150B pneumatic roller for two more passes, for a total of five passes.
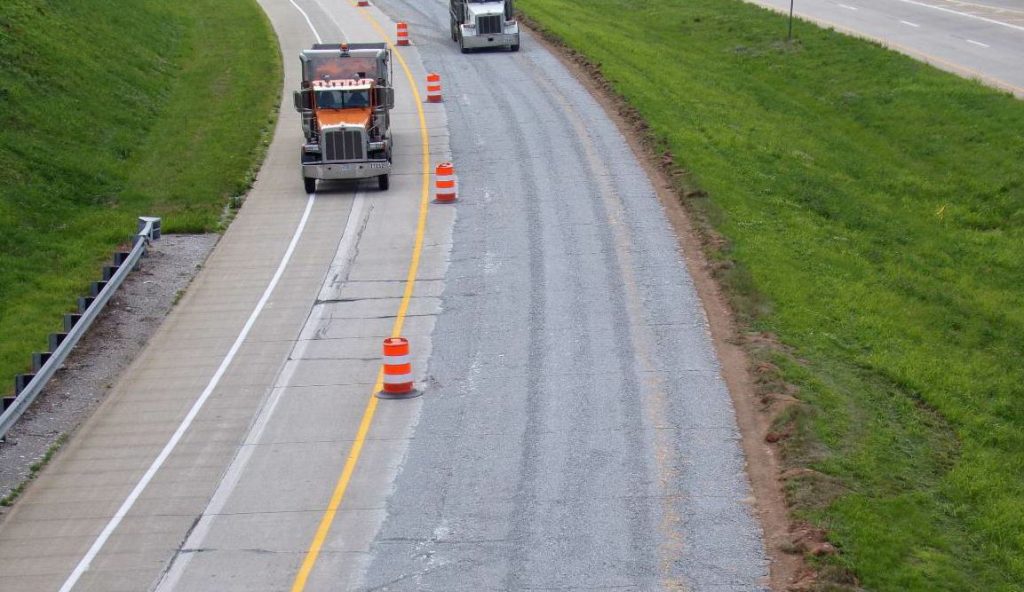
Rubblizing the job allowed the department to utilize the crushed concrete as a structural base and drainage layer, said Ken Arthur, Boxley’s Asphalt Plant Operations Manager.
Boxley did encounter some challenges with traction of equipment on the rubblized base.
“When we put the paver on top of the rubblized material, it was like paving on marbles,” Pieklik added.
To prevent slipping, Boxley informed their haul truck drivers not to accelerate too hard on the surface and instructed the crew to pay attention to places affected by twisting, turning or acceleration of equipment. For this, they placed additional crew members to repair piles of moved material ahead of the paver and shuttle buggy.
Boxley used a Roadtec 2500A shuttle buggy to load the paver. This put less weight on the paver–a Roadtec 190E–which didn’t need to push any fully loaded trucks down the road.
On the ramps, they paved with a PROPAVE 110RT track paver to distribute the weight better on the steeper grade.
For the main line, Boxley’s crew paved 4 inches of BM-25.0D + 0.8 with 5.2 percent liquid AC directly on top of the rubblized concrete. “The BM-25.0D +0.8 mix is our highest-binder base mix in Virginia,” Arthur said.
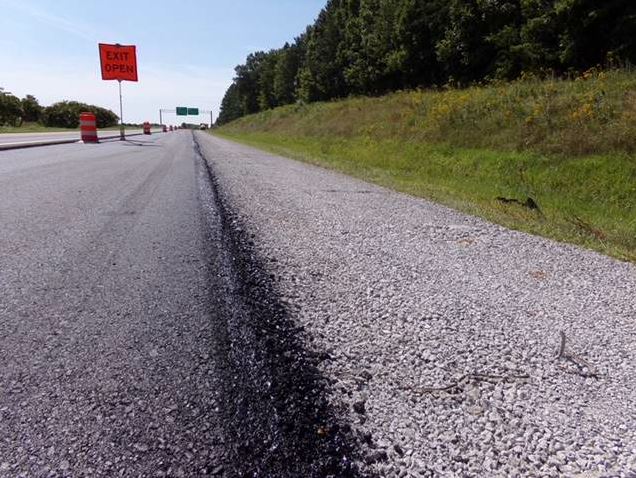
The majority of the project was rubblized to a depth of 12 inches in the main travel lanes and 9 inches on the shoulder, covered with a 4-inch base lift, 2 inches of IM-19.0D and then 2 inches of SM-12.5D, for a total of 8 inches of asphalt paved in three lifts.
“We knew traffic would be released onto the new base and binder layers prior to the final surface and we wanted to make sure it didn’t rut,” Arthur said. VDOT performed internal rut-testing on the same mix on another project earlier this year and the results came back very positive, Arthur said. “That gave them the confidence to utilize the spec for this project.”
Another benefit of the high binder base mix immediately on top of the rubblized concrete is that it is less prone to stripping than conventional base.
On top of the 4-inch base lift, Boxley paved 2 inches of IM-19.0D and then 2 inches of SM-12.5D, for a total of 8 inches of asphalt paved in three lifts.
“With the exception of the high-binder base mix, this was a standard heavy-duty pavement design structure for the volume of traffic we see in this district,” Blount said.
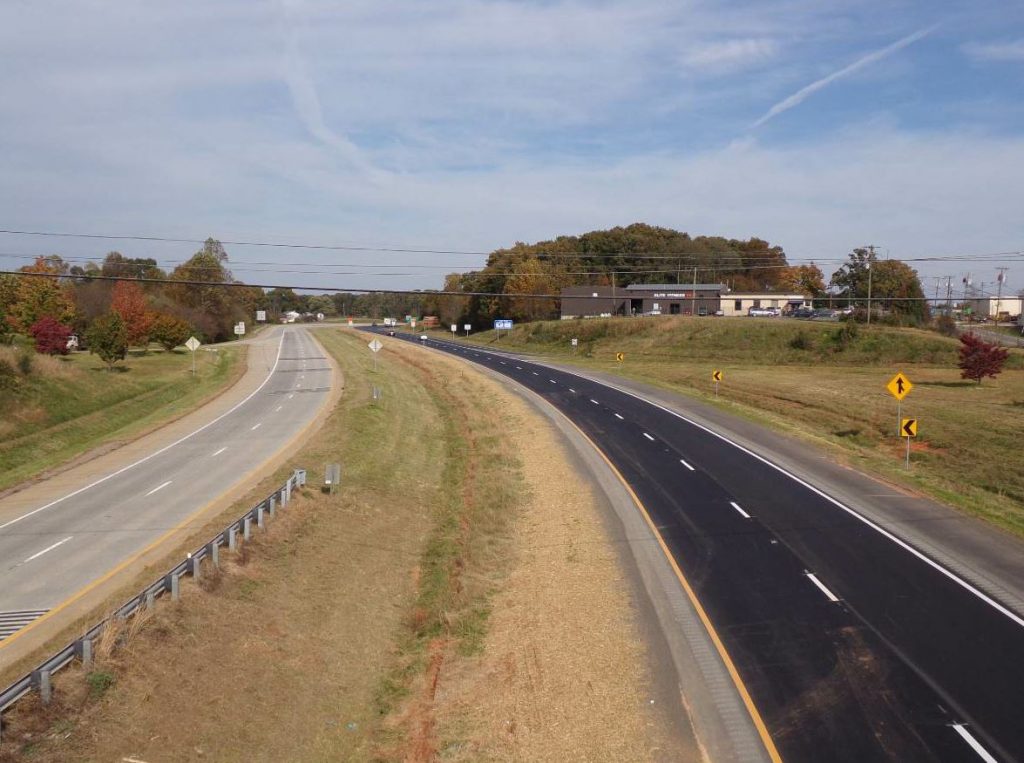
The 2.6-mile project on Route 460 included the rubblization of the existing concrete roadway and the placement of a new asphalt overlay.
Due to vertical clearance issues at the three bridges along the project, they did a full removal and replacement with new base stone at the bridges. The 7-inch full-depth removal under the bridges was replaced with 9 inches of 21A stone material, then 7 inches of the same high binder base mix, 2 inches of IM-19.0D and then 2 inches of SM-12.5D for a total of 11 inches of asphalt paved in four lifts.
In total, Boxley laid a total of nearly 33,000 tons of asphalt: 17,000 tons of base mix, 8,000 tons of intermediate mix, and 7,900 of surface mix. All of the mix produced was warm-mix asphalt with 26+ percent RAP, produced at Boxley’s Astec double barrel 300 ton-per-hour Lynchburg plant 15 miles from the project.
For the job, they’re performing typical VDOT testing, which includes volumetrics, gradation, and asphalt content testing in the lab and density in the field. The average densities on the base layer hit around a 97.5 percent. “That’s huge,” Arthur said. “VDOT has been particularly pleased with field densities achieved on the high-binder base.”
Boxley received a bonus incentive for completing the project 34 days early. They also received a rideability bonus on both 2.6-mile lanes, which had final average IRI numbers of 60.4 and 58.5.
“Replacing a well-known concrete section was a very high-profile job for our area,” Arthur said. “We were excited to see VDOT utilize an asphalt application and partner with them in making it successful.”