Intercounty Paving Dives into Intelligent Compaction
BY Tom Kuennen
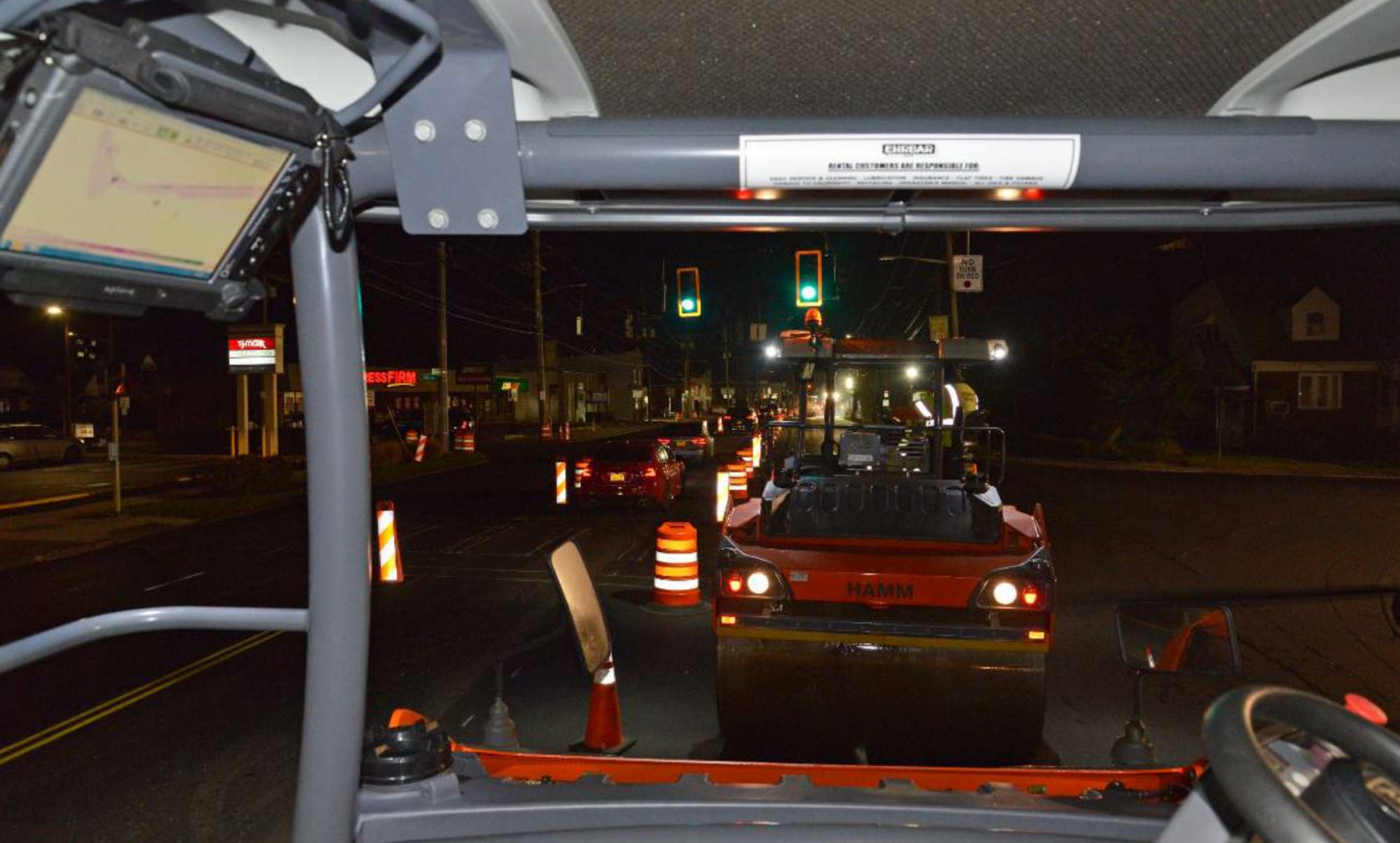
When New York State Department of Transportation (NYDOT) specs began requiring intelligent compaction (IC) technology for asphalt paving, a major paving contractor in the Northeast got into it in a big way, acquiring eight new articulated tandem rollers equipped with IC systems.
The Hamm tandem rollers from Hamm, a division of Wirtgen Americas, Antioch, Tennessee, were each outfitted with Hamm Compaction Quality (HCQ) technology, incorporating the Hamm Compaction Meter and Hamm Temperature Meter within the Hamm Navigator system.
As AsphaltPro readers know, IC—as it applies to asphalt and soil compaction—describes compaction of road materials using rollers equipped with an integrated measurement system, an onboard computer reporting system, GPS-based mapping, and optional feedback control, according to Federal Highway Administration consultant The Transtec Group, Austin.
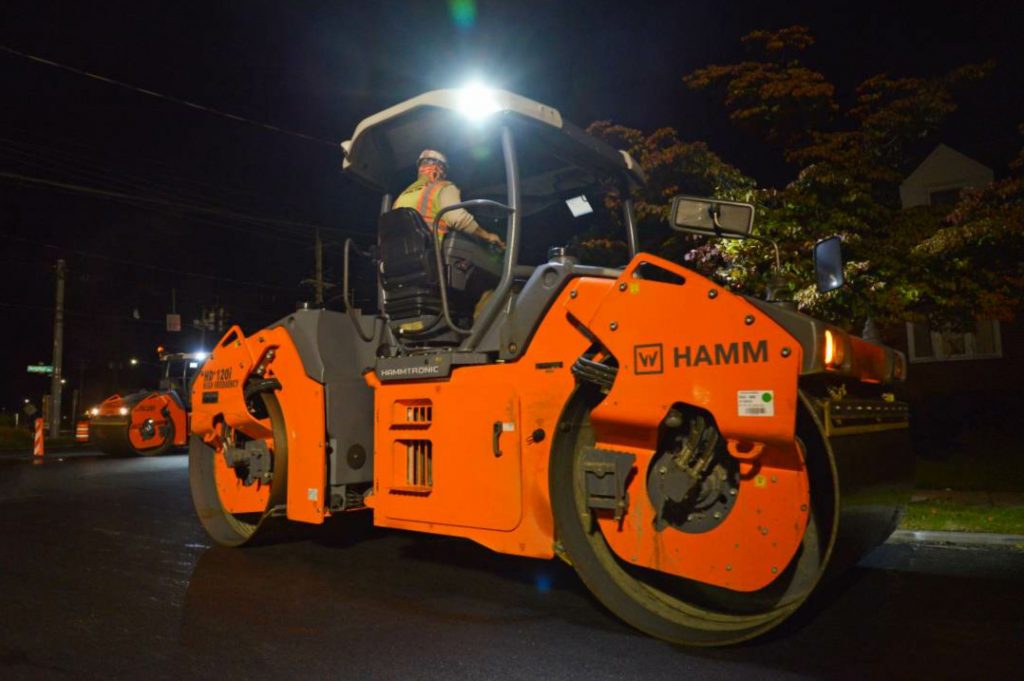
The Hamm Compaction Meter measures the stiffness of asphalt or soil beneath the drum, and consists of an accelerometer mounted on the drum framework inside the rubber buffers, a processor and a display. With the accelerometer mounted this way, users get the actual reaction of the drum against the material it is compacting. Based on these data, the processor calculates the HMV (HAMM Measurement Value) – indicating the degree of compaction as a stiffness measurement derived from the measured signals – and displays this value to the driver in the cab.
IC rollers allow real-time compaction monitoring and timely adjustments to compaction by integrating measurement, documentation and control systems. IC rollers also maintain a continuous record of plots (typically color-coded), allowing the operator to view plots of the precise location of the roller, the number of roller passes, mat temperature, and material stiffness measurements.
Intercounty Paving Associates LLC, Westbury, New York, was using its new rollers with HCQ Navigator on State Route 24 (Hempstead Turnpike in Nassau County) in the shadow of Belmont Park race track, and on the Saw Mill Parkway in Westchester County north of New York City.
Hempstead Turnpike
On Hempstead Turnpike, in a congested urban location in central Long Island, Hamm HCQ Navigator system components were mounted on two HD+ 140i VV-HF rollers, and one on an HD+ 120i VV HF tandem roller. A third HD+ 140i VV-HF HCQ Navigator system-equipped compactor was on location as a backup. On the Saw Mill Parkway project, two new 140s and two 120s were used. On these projects the 120s are used for main line paving, but also intersections and radii.
On New York State Route 24, Intercounty spent two weeks repairing the pavement, resetting castings, and replacing deteriorated concrete panels beneath the existing asphalt layers. Frank C. Lizza Jr., general manager for Intercounty, explained that the crews milled out a lane and immediately paved behind it each night during the mill-and-fill phase.
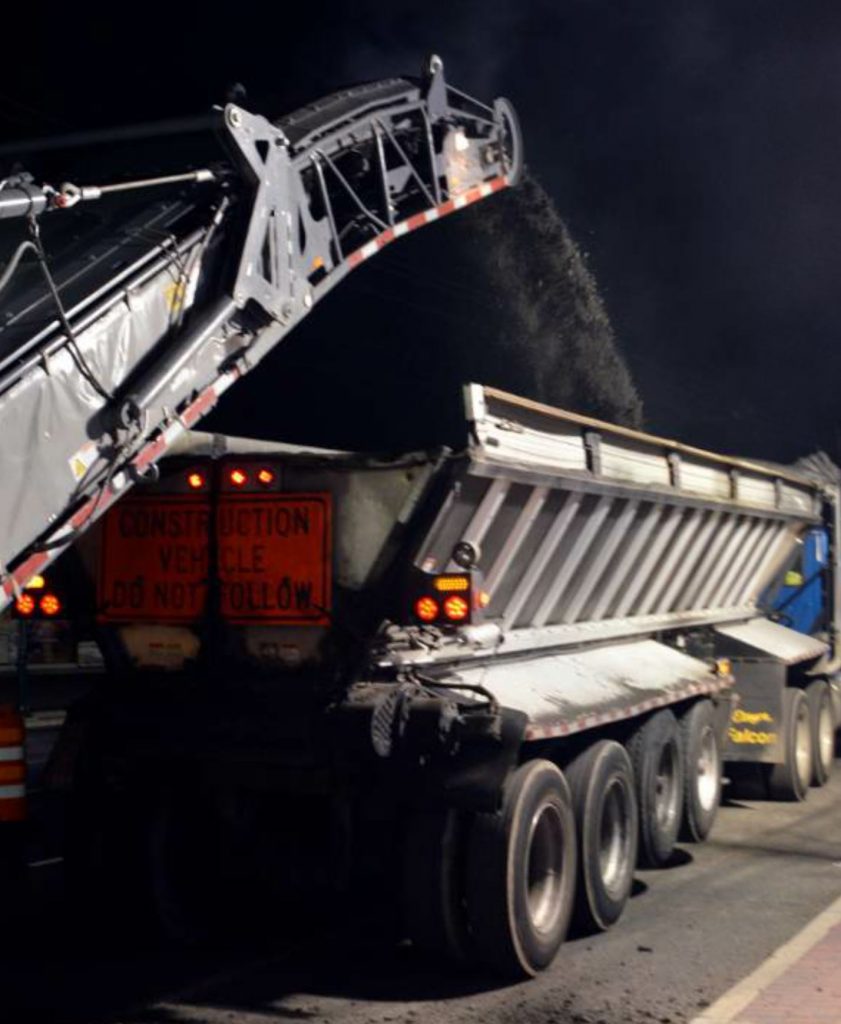
Intercounty Paving Associates LLC, Westbury, New York, milled 13 lane miles over a 2-mile distance. Photos courtesy Hamm, a division of Wirtgen Americas
Using two new W 250i cold mills, Intercounty was milling 2 inches, then placing 2 inches of 9.5 mm NMAS PG64E-22 Superpave mix as a single driving course, all in one night. The mix contained a polymer modifier and asphalt content ranged from 4.5 to 5 percent. “Our 9.5 mm mix is approximately 60 percent 1/4-inch material, and 40 percent stone sand,” Lizza said. “Granular material includes 20 percent reclaimed asphalt pavement (RAP).”
The Route 24 project was being done in phases, beginning in mid-October 2017 and continuing into June 2018. The early November segment involved 13 lane-miles over a 2-mile distance. Each night, Intercounty was milling 2,200 tons of RAP, and replacing with 2,200 tons of asphalt mix. In total 18,000 tons of asphalt was milled and placed in this segment.
Granite Construction Models Success with Intelligent Compaction
Milling of the approximately 15- to 16-foot-wide lanes was done by a W 250i with 12.5-foot drum, followed by a W 250i with 8-foot drum picking up the remaining width along the curb. Milling moved forward at 100 fpm.
“RAP is delivered to our facility in Cedarhurst,” Lizza said. “Up to 20 percent will be re-incorporated into this mix, and the rest barged up the Hudson River to other facilities, where it will be sold.”