Cherry Point Airfield Project Success Story for S.T. Wooten
BY Chris Croom
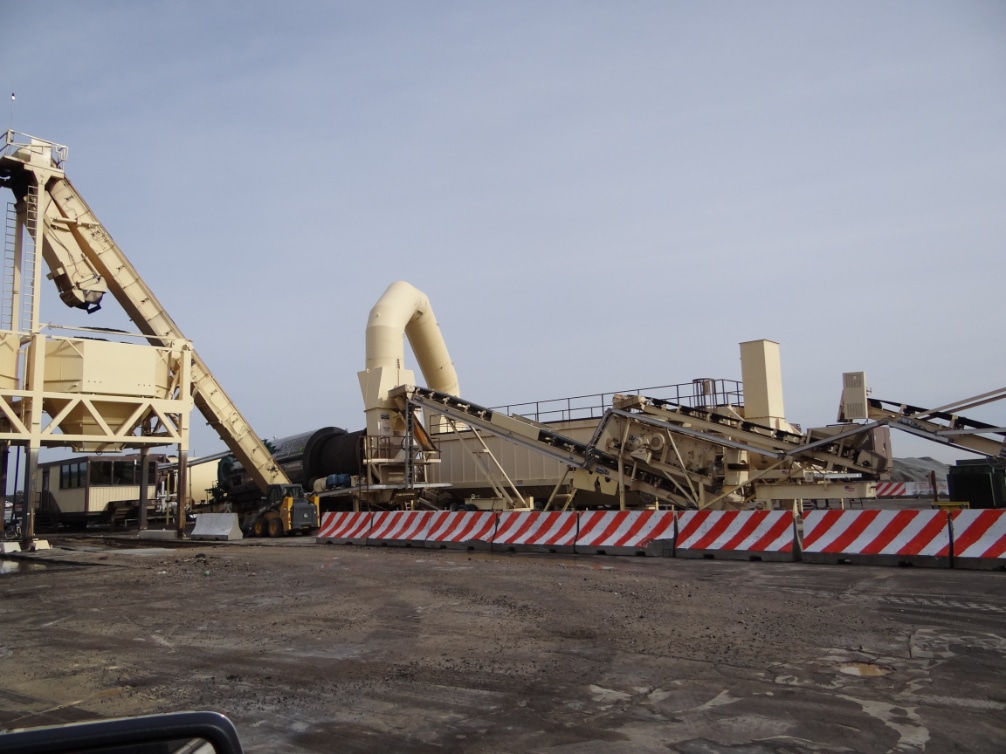
Teamwork was the recipe for success on S.T. Wooten’s paving project at the Marine Corps Air Station (MCAS) Cherry Point in Havelock, North Carolina. Tasked with repaving several runways and taxiways at the airfield, crews collaborated closely to execute in the short turnaround between departure and arrival time for the finished job.
Crews from S.T. Wooten’s asphalt and commercial divisions along with various subcontractors worked together to ensure a smooth landing for the project. Thanks to their hard work, the project was recognized with a national honor for excellence in airport paving—the National Asphalt Pavement Association’s (NAPA) 2022 Ray Brown Asphalt Pavement Award.
S.T. Wooten was hired as the turnkey contractor to manage and execute all construction activities for the Cherry Point job. While the project was given a tight timeline, the company’s previous experience on runway mill and overlay projects at the same airfield was beneficial on this project.
Building the Itinerary
The military hires construction companies through a Multiple Award Construction Contract (MACC) process which calls upon larger, pre-qualified general contractors to submit for and oversee projects. This system helps streamline the paperwork and increase efficiency. Historically, it could be a tedious process to ensure contractors align with all the federal requirements to work on a military base.
Daniels and Daniels Construction was selected as the prime contractor to oversee the Cherry Point project and S.T. Wooten was hired as the turnkey subcontractor to manage and execute all construction activities. While the project was given a tight 570-day timeline, S.T. Wooten’s experience having previously worked on resurfacing projects at the same airfield came in handy.
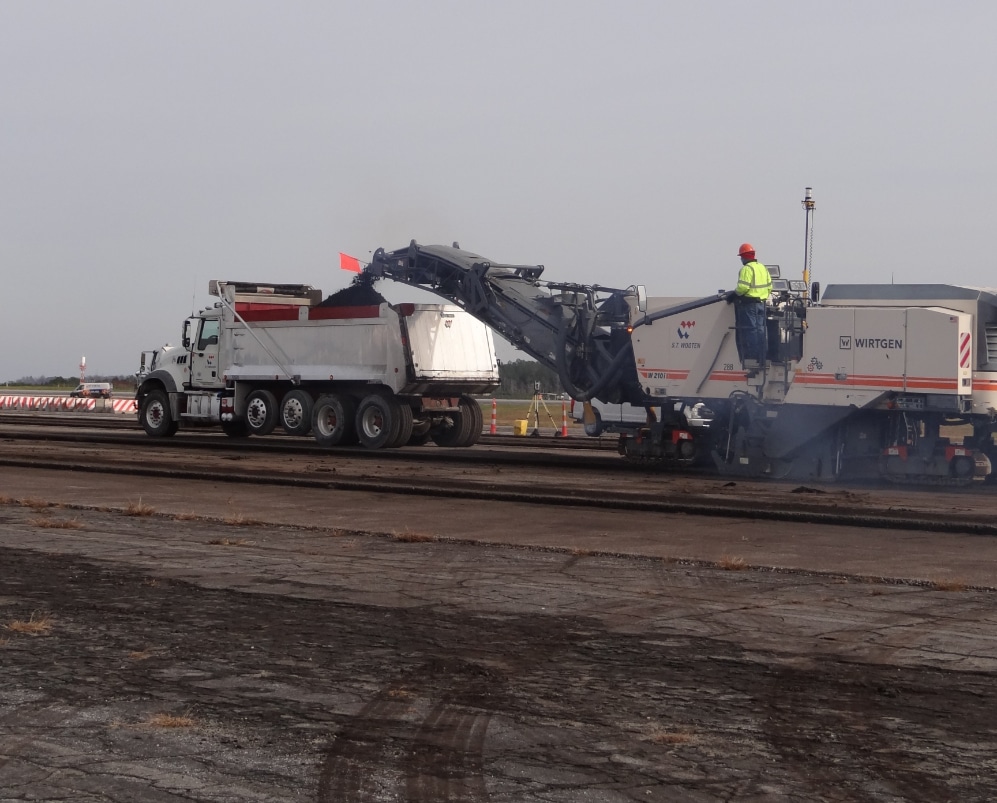
The Wirtgen machine-control technology used the 3D model to mill and cut to the proposed grade.
Readying for Takeoff
Crews understood that there was pressure to put the Cherry Point job on a fast track given the short timeframe to complete the project. Contracts were not finalized until mid-September 2021 and the base’s leaders wanted to get some paving done before the end of the year. Managers had to begin strategically developing schedules for not only milling and paving but also other subcontractors.
To expedite the process, S.T. Wooten moved a portable plant onto the base so crews could deliver asphalt as quickly as possible to the runways. A total of 53,470 tons of hot-mix asphalt was placed for the project. The asphalt plant came from the company’s Garner, North Carolina, location and was returned to that same site at the completion of the project. The same plant has been used to support the I-40 road widening project that is in the works between nearby Raleigh and Clayton.
Making the Shift on S.T. Wooten’s I-40 Road Widening Project
Gaining Altitude
Paving work is always done with precise measurements in mind, but being exact is even more important for runways and airplanes. For Cherry Point, the military required that the finished pavement had to be within 3/100s of an inch of the plan’s elevations.
To help achieve such an exact standard, S.T. Wooten utilized a Wirtgen milling machine with 3D machine control. This is the same approach used in GPS-controlled grading and earthmoving equipment; here, those same 3D models were used for machine-controlled milling to both the exact grade and slope needed.
S.T. Wooten started by surveying the existing elevation on each runway.
- The measurements were compared to the project plans, which proposed a new finished elevation. The crews couldn’t simply mill and replace the pavement in the exact same way; the entire runway needed to be reprofiled.
- Senior GPS Engineer Danny Wrench used the project plan to create a 3D model of those new elevations.
- The Wirtgen machine-control technology used the 3D model to mill and cut to the proposed grade. This helped ensure the milled surface matched both the new grade as well as milling down to the level required. In this case, that was two inches below the proposed finished elevation.
A second elevation survey was done to ensure the newly profiled and milled surface matched the project specs. This post-mill survey had to be submitted for approval by the government or architect/engineer before the next step.
Crews then paved the 2-inch surface course. A third and final survey confirmed that the final surface elevations were within the 3/100s of an inch of the plan’s specifications.
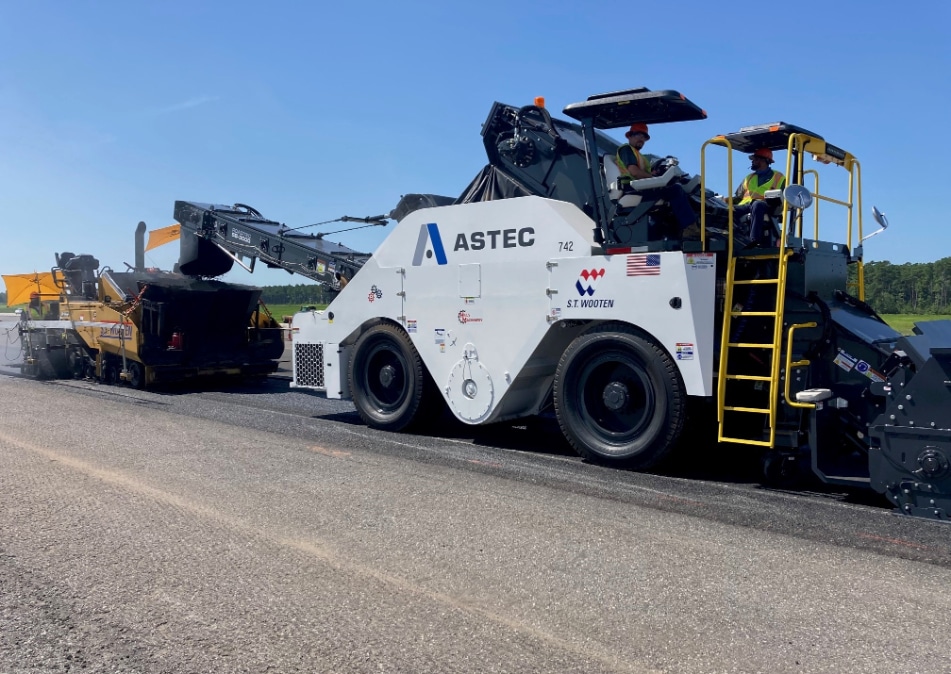
Crews paved the 2-inch surface course prior to a third and final survey confirming the final surface elevations were within the 3/100s of an inch of the plan’s specs.
Prepared for Turbulence
While 3D modeling helped crews ensure accuracy, the unexpected realities of a work zone can always throw a wrench into plans. One obstacle with the Cherry Point job emerged when it came time to change out the existing pavement profile, which consisted of an old layer of paving fabric that was installed between asphalt lifts. The fabric was not always in the exact location it was supposed to be, which caused milling and paving to take longer than expected.
The team took some troubleshooting measures to help clear the hurdle. Crews performed additional milling in locations of the runway where uncertainty existed to ensure any fabric they encountered was completely removed. Then they placed a new leveling layer of asphalt and re-milled the leveling course to the required pre-pave elevation per the 3D model.
Changes in Flight Path
In addition to some execution challenges, there were changes in the project plans that called for crews to pivot. For paving, a Michigan Wedge technique had traditionally been used for runway construction at the base—involving the creation of a 45-degree slope on the asphalt edge and joining lanes with a joint heater. The Cherry Point project had initially called for a similar strategy, but specs were updated to require a saw-cutting technique.
A subcontractor was hired to perform the saw cutting, which helps ensure a tight connection between lanes. However, the process—combining saw cutting and milling—was one that crews also had to monitor stringently as it can be somewhat messy. Crews were constantly cleaning up foreign object debris (FOD), which is airfield jargon for dust, bits of pavement and rocks. While these small bits might not seem like a big deal, they are especially important to manage on airfield projects where too much dust can cause costly problems for jet engines.
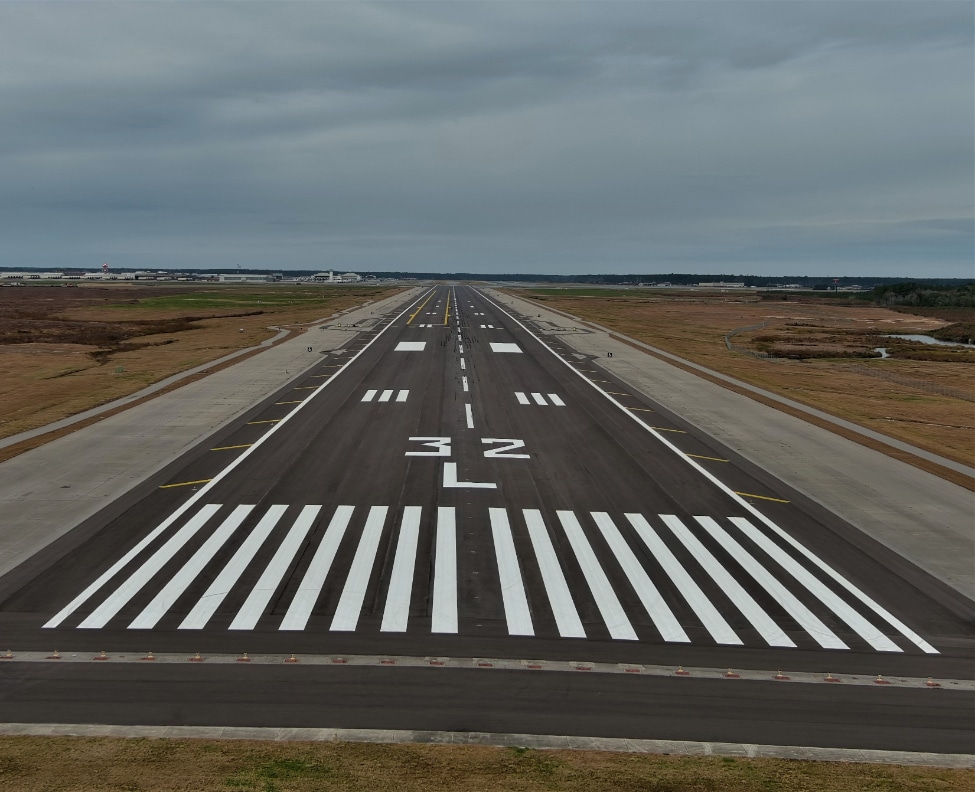
The Marine Corps Air Station Cherry Point project garnered a 2022 Ray Brown Asphalt Pavement Award for S.T. Wooten.
A Successful Landing
Despite a rushed start and some changes to the project specs, roughly half of the work was completed before Christmas 2021. That gave crews a long runway to finish the paving when the weather was warmer in the spring and summer 2022. It also meant that crews mostly had to deal with reinstalling the lights and finishing the lane markings toward the end of the project.
Having runway experience helped the team successfully fast-track this project and ensure they safely and successfully met each milestone along the way. Collaboration and hard work also propelled the project to its scheduled completion date. The results will allow a smoother landing for aircraft in the years to come at Cherry Point airfield.
And thanks to the great work conducted by all the crews involved with the project, S.T. Wooten was proud to put some new hardware in the trophy room with its NAPA Ray Brown Award recognition.
Chris Croom is the division manager; materials and quality control, S.T. Wooten Corporation.